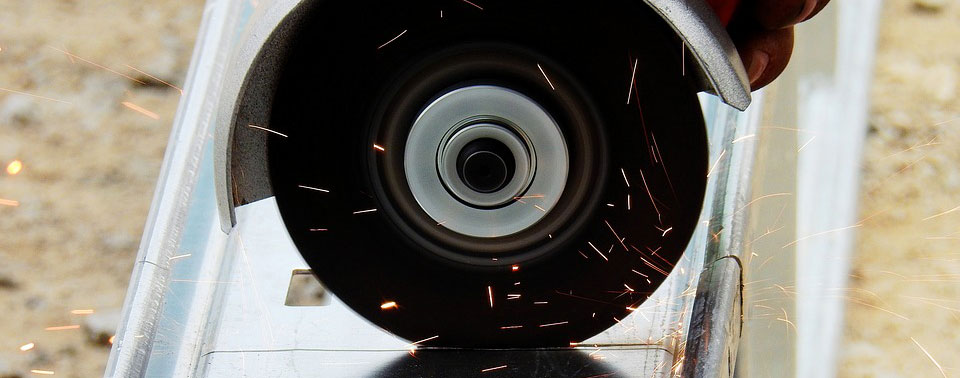
Grinding Wheel Dressing Method
The long life grinding wheel dressing method:
Wheel dressing is generally done by turning, using diamond rollers, grinding and rolling.
- 1. Turning dressing method: Single-grain diamond is used as a tool to turn the grinding wheel, which is the most common dressing method. The diamond cutter mounted on the tool holder is usually inclined by about 5° to 15° in both the vertical and horizontal directions; the contact point between the diamond and the grinding wheel should be 0.5 to 2 mm below the axis of the grinding wheel, and the diamond is evenly lowered at the time of trimming. Give the move. The smaller the surface roughness after grinding is required, the lower the feed rate should be.
- 2. Diamond roller dressing method: a diamond roller made by injecting a large amount of diamond particles on the surface of a steel roller by electroplating or powder metallurgy, rotating at a certain rotation speed, causing grinding and rolling action on the surface of the high-speed rotating grinding wheel, so that The long life grinding wheel achieves a sharp working surface that fits the roller profile. Diamond wheels are complex to manufacture and costly, but they are durable and have high dressing efficiency. They are suitable for dressing grinding wheels for special forming surfaces in mass production.
- 3. Grinding wheel grinding and dressing method: the ultra-hard-grade silicon carbide grinding wheel with low-speed rotation and the high-speed rotating grinding wheel are used to achieve the purpose of dressing.
- 4. Rolling dressing method: using a carbide disc, a set of rollers made of wavy white iron discs or grooved hardened steel sheets, and grinding and pressing of the long life grinding wheel. The roller is generally mounted on the trimming fixture for manual operation, and the trimming efficiency is high, which is suitable for the dressing of the coarse grinding wheel.